Innovative Prefabricated ADUs of the Future
The humble “granny flat,” that small home out in the back yard, has gone from an after-thought to a model of innovation, with prefabricated accessory dwelling units giving homeowners the option to complement need with affordability, style, sustainability, and ease. Typically, accessory dwelling units, or ADUs, are built in place like other home construction, after property owners obtain the necessary building permits and design approval from their local jurisdictions.
ADUs are one of the hottest topics in real estate, projected by many to potentially become a large part of the future housing. “In the places that have allowed these (ADUs) by building permit for a time, as much as 20 to 25 percent of the housing stock in these communities has an ADU. In California, we have 7 million single-family homes. If 20 percent of California homes had an ADU, that would be (1.4 million) places for people to live. So, the potential impact at the state level is enormous,” said Denise Pinkston, Board President of the Casita Coalition.
The approval process though, depending on the city or county, can take months before building even begins.
Then, construction itself can take many more months of noise, dust, and disruption.
Prefabricated ADU Manufacturing
But a group of manufacturers is working to change all that. Using innovative technologies, processes, and materials, these builders can place – or unfold – a fully functional, well-designed, lower-cost ADU on a property and have it up-and-running in no time.
These unique ADUs are Prefabricated, or Prefabs as they are often called. Market innovators are betting on them having the potential of being as much as half of all new ADUs constructed. While the United States has been slow to adopt prefabricated housing, other nations like Sweden have embraced them more wholly. In fact, as much as 70 to 80 percent of housing in Sweden has prefabricated elements. While larger single-family homes in the United States may be a slower to adopt prefabrication, one clear market opportunity for prefabricated homes is with ADUs.
Prefabricated ADUs run the gamut, but in general, they are built almost to completion in a factory and shipped to the site for the final assembly. They are then hooked up to the foundation and utilities, and are ready to go.
While prefabricated ADUs have been around for a while, 21st century materials and processes are innovating the industry and propelling it into the future, changing prefabs from stick-built small homes to truly futuristic feats of design and engineering.
A number of these innovative companies are working to build comfortable, energy-efficient, strong units that can provide much-needed affordable shelter anywhere in the world. ADUs are viable as a solution to housing shortages – especially low-cost housing — homelessness and letting an aging population stay independent as long as possible.
California, which has some of the nation’s most stringent building codes, has made a concerted effort to facilitate the building of ADUs to alleviate housing issues.
CALIFORNIA: LEADING THE WAY >> LEARN HOW CALIFORNIA’S LEGISLATURE HAS LEGITIMITIZING – POPULARIZED – ADUS
As is the case in many states, California’s Housing and Community Development department must sign off on factory-made ADUs and ADU components because often things that would normally be inspected on-site, such as electrical wiring, are sealed up out of sight before the unit ever leaves the factory. Situating their factories in or near California and receiving certification from the state that acknowledges the safety of their products, these builders are crafting units that truly can go anywhere, fast. While these companies are focused on manufacturing, they aren’t leaving everything to property owners to figure out. The builders below partner with a range of professionals to help homeowners navigate a jurisdiction’s permitting processes, and the on-site construction aspects of placing an ADU, such as pouring a foundation and extending utilities from the main house.

A recycled house?
Repurposing used shipping containers as ADUs might not seem all that comfortable. But the large boxes, made to hold 65,000 pounds and stack 10 containers high, provide a strong and stable shell for a warm and inviting home.
Conceptualized and developed by Keith Tantilinger in the 1950s, the modern “intermodal container” was created to allow for end-to-end shipping of containers via vehicle, ship and even rail without having to continuously load and unload them. Essentially, a revolution for shipping and logistics. Today, experts estimate there are over well over 17 million metal shipping containers around the world, with at least 6 million currently in use. That is a lot of steel that is potentially reusable in a sustainable way.
Carson, Calif.-based CRATE Modular fabricates buildings out of repurposed shipping containers, including homeless shelters, apartment buildings, and now, ADUs.

“I have a background in affordable housing, so I am incredibly passionate about housing as a general rule,” said Amanda Gattenby, vice president of development with CRATE Modular, and the person who started the ADU portion of the business. “I do think that by doubling the density on single-family lots with ADUs, there can be a big impact to homelessness, for people aging in place longer, for people to have a caretaker be able to live with them, for kids that failed to launch or are coming back after college, and home health workers, or just an income tenant.”
To make that happen, CRATE sources containers before their maiden voyage and uses only those that travel one-way carrying dry goods. Each container has a serial number that allows it to be tracked, and lets CRATE know what exactly what it carried. Each container is tested when built, then CRATE does further testing.
They’re very, very safe,” Gattenby said. “They’re actually more heavily tested and rigorously inspected than typical building materials.
To change a shipping container into a comfortable home, CRATE makes a number of modifications, many of which are geared toward sustainability. Energy efficiency comes through significant insulation, quality glazing on windows, energy-efficient lighting and mechanical systems, and a TPO roof which helps keep the indoors cool. Building in a factory helps to reduce on-site waste. It also decreases the noise and disruption in the neighborhood that comes with traditional construction onsite when building in place. Additionally, the largest part of the structure is recycled. Buyers also can choose a variety of finishes to make the home their own, including Corian wall panels in the bathroom, quartz countertops, soft-close drawers, Kohler and Moen fixtures.
CRATE works with brokers to discuss options with the homeowners and to identify others in the area who can prepare the permits and the site. When the unit is ready, the general contractor uses a crane to lift it over the main house, if necessary. Then it’s just a matter of securing the unit to the foundation, hooking up utilities, and a few other last items before the unit is ready to go. The single-container units can be set up and slept in on the same day.

Hot off the printer
3D printing and homes might not seem to go together, unless a printer is used to create an architect’s model of a home. Usually 3D printers are used for smaller applications like prototyping products or creating art. However, one company is working to revolutionize their use in mainstream construction.
That’s right. Oakland, Calif.-based Mighty Buildings 3D prints panels that serve as part of an ADU or they’ll print the entire module.
Set-up speed is an important factor in factory-built prefabricated units. Another is affordability.
When it comes to comparable quality, we’re about 40% less than equivalent stick-built,” said Sam Ruben, chief sustainability officer and co-founder of Mighty Buildings, a construction technology company that uses 3D printing, robotics and automation to bring customers low-waste, energy-efficient, comfortable units.
Mighty Buildings uses 3D printing for the most difficult, dangerous parts of the build, such as framing, Ruben said. Then they use robotic post-processing to scan the printed objects to make sure they match the model.
Using software also gives the manufacturer the ability to switch from one building design to another simply through some tweaks, without having to reconfigure the production process. That will allow custom designs in the future.
Mighty Buildings’ ADU can be manufactured while the site is being prepared. While the company offers just the units, it also provides a full turnkey option, where it coordinates the entitlements and the general contractor, making things easier on the homeowner. The units, when ready, can be hoisted over the main house using a crane.
In addition to making units more affordable and faster to deliver, using 3D printing, robotics, and automation to manufacture ADUs helps with quality control, decreases on-site disruption and allows for a more sustainable production process.
“We’re also able to do practically zero-waste construction, because we only print exactly what we need,” Ruben said. Even the powder from the milling process doesn’t go to waste, as the company captures it and reuses it as filler.
Mighty Buildings is motivated to manufacture ADUs as a viable solution to the housing crisis, adding density to a neighborhood without really changing its character.
“It’s too expensive for people who serve our communities to live in our communities,” Ruben said. “And that’s something I think we could change.”
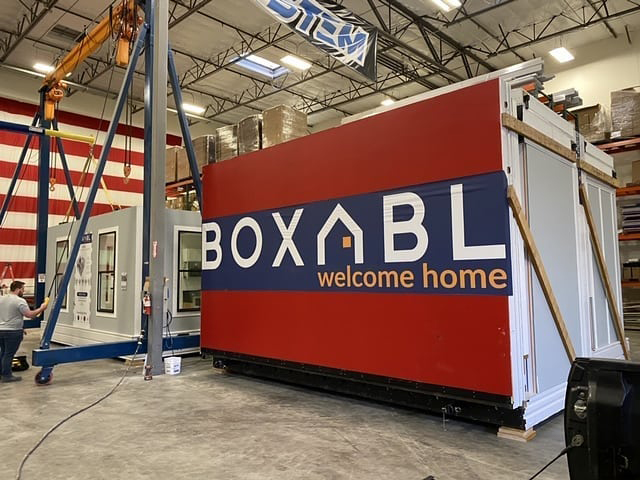
The future unfolds
Like high-tech origami, Boxabl has taken folding to new levels.
The Las Vegas-based company can tow what looks like a regular rectangular box to a property, place it on a foundation, and in a matter of hours, unfold it into a casita that’s ready to be lived in.
The impetus behind an unfolding factory-built ADU was to maximize efficiency, decrease costs, and increase quality, taking a page from modern mass production.
“All our modern products are built in a factory on an assembly line, a lot of them using advanced automation and robotics,” said Galiano Tiramani, head of business development for Boxabl, as well as its owner and founder. “Except housing. So, as a result, there’s a shortage of housing. It’s high cost. But there’s no shortage of cars or iPhones or sneakers. So it’s a no-brainer. This stuff needs to move into the factory so that they can have efficient assembly lines and mass production.”
When folded, a Boxabl ADU that would be 20-feet wide when unfolded can ship compete with a finished kitchen, bathroom, electrical wiring and HVAC, and still be only 8.5 feet wide, meeting standard highway shipping size. That means a Boxabl unit can be towed by a pickup truck, and cuts down on transportation costs because it’s not an oversized load.
Bringing ADU construction into the factory means greater quality, safety, and efficiency, Tiramani said.
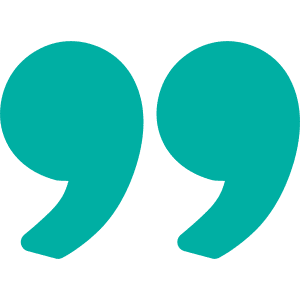
– Tiramani
And the units are engineered to be used around the world, able to withstand, for instance, high winds, fires, and earthquakes. They can also be used as shelters in disasters.
Boxabl is working on other contracts at the moment, but expects to be open to the public within a year, and will work with partners to help homeowners with permits, financing and onsite, work.

An operating system for your home
Operating systems run our cell phones and computers, but did you know one could run your home? Or, in this case, your ADU.
While it’s not unexpected for a homeowner to be able to control lights and security systems from a cell phone, those systems are typically added on after construction, and placed only in certain areas of the home. They allow for some control, but it’s generally not throughout an entire home.
Veev, a California-based real estate development company, has taken the operating system concept from the smartphone to the smart home, outfitting its ADUs during manufacturing with technology that allows people to control their homes from a smartphone or wall app.
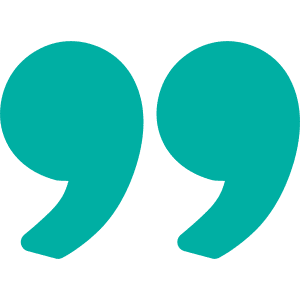
– Kelly Hampton, Vice President of Marketing and Sustainability for Veev
Encasing the latest technology are Innovative and sustainable materials that help Veev create ADUs that are strong, healthy, and considerate of the environment. The ADUs come with solar panels and are highly energy efficient. The company uses primarily steel and high-performance surface, a customizable surface that is non-porous, hygienic and easy-to-clean, and that is mold, bacteria, moisture, and termite resistant.
“Leftover parts from the manufacturing process are then reused and repurposed or recycled. This has allowed us to create a near-zero waste system – 99 percent of Veev’s generated waste is reusable or recyclable,” Hampton said. “Additionally, Veev’s high-performance surface (HPS) is also GREENGUARD Certified, guaranteeing that we create a non-toxic, chemical-free, indoor living environment in our new homes.”
As many of the builders indicate, bringing the manufacturing of ADUs into a factory allows for greater quality control, more efficiency, and increased production speed. Veev has recently achieved a building speed four times faster than the industry standard.
That speed helped the company produce 78 units in 90 days for the City of San José, allowing those experiencing homelessness or displacement due to the COVID-19 pandemic a home.
Just because the ADUs are built quickly doesn’t mean they sacrifice comfort or quality.
“The end result: a durable, quality, and cost-effective home that gives ADU buyers a curated experience,” Hampton said.
The future of ADUs seems bright. With more people working remotely, students attending school in their own homes, and others needing affordable housing after job loss in a pandemic economy, prefab ADUs — especially those using innovative technologies, processes and materials – are poised to offer a lower-cost, sustainable, comfortable place to call home.
Main Feature Image by Mighty Buildings